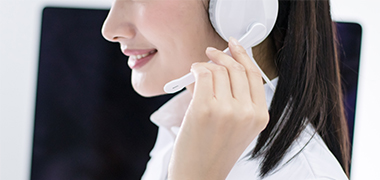
- Contact:Minister Xu
- Mobile:13841408476
- Tel:024-44837288
- Fax:024-44837004
- E-mail:xuming58@126.com
- Web:m.natashaterry.com
- Address:No.110 XiangHuai Road
Benxi Economic Development Zone
Liaoning Province
Taking the heat: grease-free bearings in baking
20 Aug,2018
Subjecting bearings to high temperatures and high levels of humidity increases maintenance requirements and costs. Also, limitations of available grease technology do not permit an increase of oven temperature that would allow faster throughput – without additional planned downtime that might offset the benefits. However, a new breed of grease-free bearings thrives in these punishing conditions – and boosts throughput.
Industrial ovens run around the clock, only pausing for maintenance. From the original equipment manufacturers (OEMs) build, who are invariably working to a budget, ovens are commonly equipped with standard bearings – lubricated with food-grade grease.
This is no design shortfall on the part of the manufacturer: as long as the bearings are maintained regularly, and run according to specifications, they will most often continue to function well. However, bakeries – and many other industrial companies – are looking to streamline their maintenance schedules in order to boost efficiency and increase profits. This is doubly important in the face of cost pressure from their customers – major food retailers.
One way to increase operational efficiency is to run the ovens faster, at higher temperatures. This increases throughput, but also puts more strain on the oven – meaning it must be maintained more frequently. Any increased profits – from baking more – can be though often offset by the cost of extra maintenance, and more frequent shutdowns.
High temperatures can be turned into an advantage
With SKF high-temperature graphite based bearings technology, customers are able to run ovens for longer without interruption, and can increase throughput while reducing downtime and cost.
Advanced graphite based lubrication generates minute quantities of graphite that lubricate the bearing during operation, preventing metal to metal contact. This is known as a ‘sacrificial’ lubrication system, as it gradually wears away to provide fresh lubricant when required. This allows the bearings to perform optimally in humid and continuous operating temperatures up to 350 C– without relubrication. Applied for standard and customized bearing solutions, this technology enables considerable maintenance savings. Listen to the testimony of a sugar wafer manufacturer.
While the high heat and humidity inside the oven combine to destroy bearing grease, these conditions are actually ideal for the replacement graphite-based system – because a degree of moisture improves the lubricity of graphite. The conditions that cause so much damage to traditional grease lubricant are actually a positive benefit for graphite.
The second factor, temperature, is simply irrelevant to graphite - graphite is generally unaffected up to 1,000°C. With this, from a bearing perspective, ovens can be run hotter in order to increase throughput.
Although the bearings are lubricated in a very different way, they have exactly the same dimensions as traditional, grease-lubricated ones – so no modification is required, and these bearings can be installed directly in place of the old ones.
This type of arrangement is usually referred to as ‘re-lubricant free’ – as the bearings are continuously lubricated by the thin layer of graphite, rather than a reapplication of traditional lubricant. And, while the bearings are lubricated in a very different way, they have exactly the same dimensions as traditional, grease-lubricated ones – so no modification is required, and these bearings can be installed directly in place of the old ones.
Learn more about graphite based technology from SKF.
Baking benefits
The most obvious advantage of this arrangement is that it reduces the need for maintenance. Because grease has been banished from the bearings, there is no need to re-lubricate them.
A typical baking oven – such as one used to make waffles – might need servicing every 16 weeks, with re-lubrication of the bearings. Graphite lubrication can help to extend maintenance intervals – or at the very least, make the regular service less arduous: a typical oven might have more than 350 bearings sets – amounting to around 1,000 bearing positions. Each one of these would have needed re-lubrication – a job that disappears with graphite cages.
This time-saving frees up maintenance staff to work on other jobs, such as those that raise machine performance – and increase profitability – rather than mere ‘housekeeping’.
The absence of grease – even of the food-grade variety – brings other benefits: enhancing food safety, by removing the risk of contamination, and there is also an environmental advantage. Before bearings are re-greased, they must be cleaned up with rags or paper towels – which must then be incinerated. A large plant will generate a huge volume of rags for disposal, but this will disappear if there is no conventional re-lubrication.
Benefits such as enhanced bearing reliability with reduced maintenance, potential for increased throughput without offsetting maintenance costs, the food safety and environmental considerations – make it a strong choice for high temperature processes like baking.