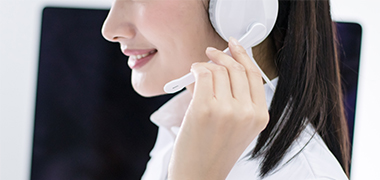
- Contact:Minister Xu
- Mobile:13841408476
- Tel:024-44837288
- Fax:024-44837004
- E-mail:xuming58@126.com
- Web:m.natashaterry.com
- Address:No.110 XiangHuai Road
Benxi Economic Development Zone
Liaoning Province
SKF Mud motor bearings cut drilling rig downtime
11 Jan,2019
Developed after extensive research, SKF’s new mud motor bearings for applications in oil and gas drilling rigs not only offer working lives up to 50 per cent longer than those of conventional products, but have also delivered a mean time between failure improvement of 30 per cent in practical trials.
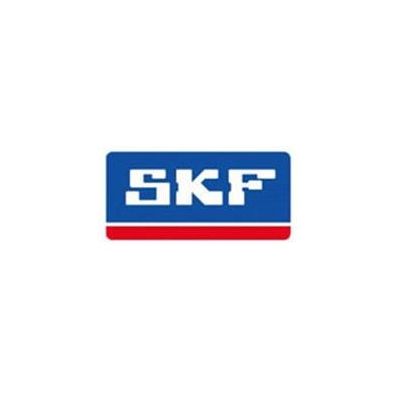
As a result, the frequency of bearing replacement is dramatically reduced and, with downtime in the region of £140,000 per day, this means that substantial cost savings can be achieved.
The key to the enhanced performance of SKF’s new mud bearings is an innovative computer model that the company has developed, drawing on its competencies in bearing behaviour and its specialised knowledge of advanced engineering materials.
For the first time, SKF’s computer model accurately defines the behaviour of mud motor bearing stacks and reveals the stress levels within each bearing. This allows engineers to rapidly carry out virtual tests on new designs, which minimise bearing stress levels while optimising load carrying capacity.
As a result of this work, SKF’s new mud motor bearings incorporate special steels for all load carrying components, and have a configuration which has been refined to offer improved wear resistance, increased load carrying capacity and greater robustness.
In addition, the new design virtually eliminates the factors which lead to cracked rings and sheared balls – two of the most common causes of failure in mud motor bearings.
SKF’s new mud motor bearings are supplied in customised versions to suit the precise requirements of each end user.
Typical models include between eight and twelve rows of bearings. When new, the majority of the load is carried by the first four or five rows but, as each row starts to wear, the load is shifted to the next row, until all the rows are worn equally.
At this point, the load shifts back to the earlier rows, and the process repeats until the bearing reaches the end of its useful life. This arrangement allows a long service life to be achieved, in spite of the extremely harsh downhole operating conditions that the bearings have to endure.