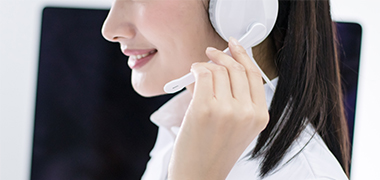
- Contact:Minister Xu
- Mobile:13841408476
- Tel:024-44837288
- Fax:024-44837004
- E-mail:xuming58@126.com
- Web:m.natashaterry.com
- Address:No.110 XiangHuai Road
Benxi Economic Development Zone
Liaoning Province
Simply better performance – Schaeffler presents various new developments
11 Mar,2019
With innovative components, ready-to-install systems, and specific Industry 4.0 solutions, Schaeffler will be presenting various new developments at the Hannover Messe, with which customers can get the maximum performance throughout the entire product lifecycle.
2019-03-08 | Schweinfurt
-
Getting the maximum performance and reducing costs for design and operation with intelligent Schaeffler solutions
-
Schaeffler supports gearbox manufacturers in reducing the number of different parts and accelerating development
-
Electromechanical linear actuators with planetary screw drives replace pneumatic and hydraulic drives
-
ProLink condition monitoring system: Multi-channel solution for condition monitoring and universal gateway for Industry 4.0 solutions
Drive technology, industrial automation, and IT continue to grow closer together. This integration offers great potential for machine manufacturers and operators to increase performance and productivity and reduce costs. According to the organizers of Hannover Messe, “Industrial Intelligence” is a decisive factor in achieving this. At Schaeffler, outstanding mechanical expertise, comprehensive understanding of systems, and decades of experience in the condition monitoring of machines and equipment are directly integrated into the development of products and systems, whether mechanically or digitally. Customers experience the added value resulting from this in the form of reduced development times for their units, higher-performance machines, more flexible and reliable production close to the maximum capacity, and additional cost savings thanks to longer maintenance intervals. With innovative components, ready-to-install systems, and specific Industry 4.0 solutions, Schaeffler will be presenting various new developments at the Hannover Messe, with which customers can get the maximum performance throughout the entire product lifecycle.
Digitalizing and accelerating the development process
Transferring gearbox models with the click of a mouse: Schaeffler has co-developed the new REXS data interface and implemented it in the company’s own BEARINX calculation program. The engineers at the trade show booth will be demonstrating how quickly and easily gearbox data can be exchanged between CAE tools and the standardized interface. Development times are thus significantly shortened and a basis created for the generation of digital twins that can be used to analyze operating data as part of Industry 4.0 solutions, for example.
Reducing the range of variants and components
Interchangeable in the same design envelope: Schaeffler will be presenting rolling bearings of different designs but with identical dimensions for modular gearbox systems. In this way, the different requirements for a bearing position regarding rigidity and load carrying capacity can be met without making any modifications to the design. The identical outside dimensions mean that special adapters and component variations (particularly for the shafts, housings, and housing covers) are no longer required. The reduced range of variants means larger quantities, lower unit costs, and shorter development and delivery times for gearbox manufacturers.
Reducing up to 90 percent in mounting times
Installing the innovative sealing solutions for profiled guide rails is child’s play: The new plastic closing plug can even be installed in a vertical position quickly and safely while the new cover strip provides free access to the fixing screws and allows alignment of the guide rail even while the carriage is still mounted. The first pilot customers have confirmed that mounting times are reduced by up to 90 percent.
25 times the operating life
Two new materials are able to withstand very high forces: Spindle bearings achieve 25 times the operating life thanks to Vacrodur’s extraordinarily high mechanical and thermal load carrying capacity, through which productivity of machine tools can be significantly increased. The maintenance intervals of extruder gearboxes can be extended from five to ten years by using carbonitrided bearings made from Mancrodur.
Integrated in a linear actuator, Schaeffler’s planetary screw drives (PWG) make a convincing case with their power density, which the example of an electromechanical riveting press illustrates. Compared with pneumatic drive solutions, an increase of up to 100 percent in output and a much more flexible process control have been realized here.
Industry 4.0 – optimizing operation and maintenance
For the first time, Schaeffler will be presenting its TorqueTracking system, which is an Industry 4.0 solution package for industrial drives. With a combination of vibration analysis and torque measurement, the drive can be operated reliably and close to its maximum capacity while maintenance can be planned and carried out based on the load conditions. This generally means that intervals are extended and maintenance costs are thus reduced.
With the new ProLink condition monitoring system (CMS), Schaeffler will be presenting its new generation of a multi-channel system for the condition monitoring of complete production facilities using four to 16 channels, for example, in the paper and steel sectors or for machine tools. In addition, the ProLink CMS can be used as a universal gateway for connecting the sensor level with the control and management levels and even cloud applications.
Detailed press releases regarding the innovations that Schaeffler will be presenting at the Hannover Messe can be found in our press kit: www.schaeffler.com/press-kit/hannover-messe
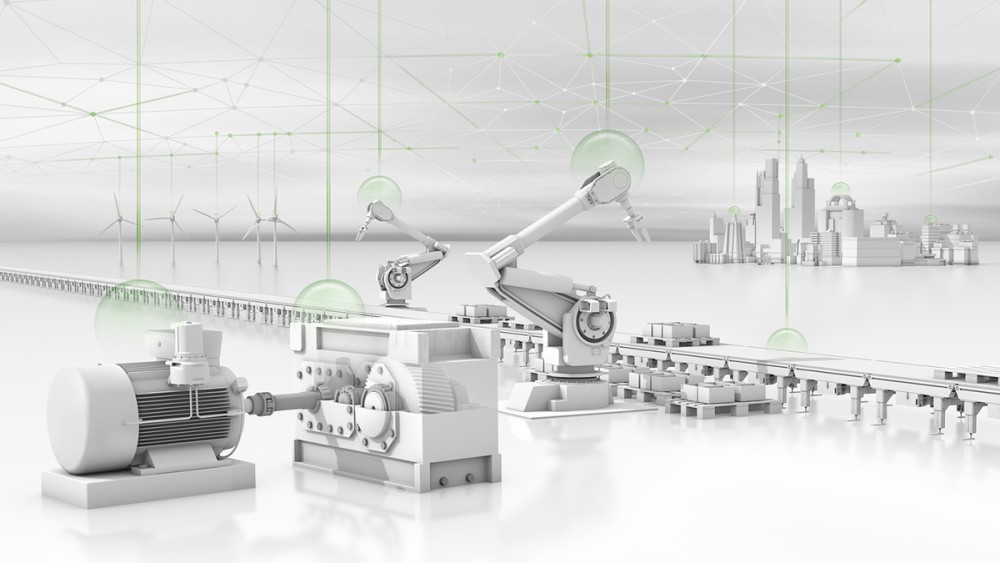
2019-03-08 | Schweinfurt
- Getting the maximum performance and reducing costs for design and operation with intelligent Schaeffler solutions
- Schaeffler supports gearbox manufacturers in reducing the number of different parts and accelerating development
- Electromechanical linear actuators with planetary screw drives replace pneumatic and hydraulic drives
- ProLink condition monitoring system: Multi-channel solution for condition monitoring and universal gateway for Industry 4.0 solutions
Drive technology, industrial automation, and IT continue to grow closer together. This integration offers great potential for machine manufacturers and operators to increase performance and productivity and reduce costs. According to the organizers of Hannover Messe, “Industrial Intelligence” is a decisive factor in achieving this. At Schaeffler, outstanding mechanical expertise, comprehensive understanding of systems, and decades of experience in the condition monitoring of machines and equipment are directly integrated into the development of products and systems, whether mechanically or digitally. Customers experience the added value resulting from this in the form of reduced development times for their units, higher-performance machines, more flexible and reliable production close to the maximum capacity, and additional cost savings thanks to longer maintenance intervals. With innovative components, ready-to-install systems, and specific Industry 4.0 solutions, Schaeffler will be presenting various new developments at the Hannover Messe, with which customers can get the maximum performance throughout the entire product lifecycle.
Digitalizing and accelerating the development process
Transferring gearbox models with the click of a mouse: Schaeffler has co-developed the new REXS data interface and implemented it in the company’s own BEARINX calculation program. The engineers at the trade show booth will be demonstrating how quickly and easily gearbox data can be exchanged between CAE tools and the standardized interface. Development times are thus significantly shortened and a basis created for the generation of digital twins that can be used to analyze operating data as part of Industry 4.0 solutions, for example.
Reducing the range of variants and components
Interchangeable in the same design envelope: Schaeffler will be presenting rolling bearings of different designs but with identical dimensions for modular gearbox systems. In this way, the different requirements for a bearing position regarding rigidity and load carrying capacity can be met without making any modifications to the design. The identical outside dimensions mean that special adapters and component variations (particularly for the shafts, housings, and housing covers) are no longer required. The reduced range of variants means larger quantities, lower unit costs, and shorter development and delivery times for gearbox manufacturers.
Reducing up to 90 percent in mounting times
Installing the innovative sealing solutions for profiled guide rails is child’s play: The new plastic closing plug can even be installed in a vertical position quickly and safely while the new cover strip provides free access to the fixing screws and allows alignment of the guide rail even while the carriage is still mounted. The first pilot customers have confirmed that mounting times are reduced by up to 90 percent.
25 times the operating life
Two new materials are able to withstand very high forces: Spindle bearings achieve 25 times the operating life thanks to Vacrodur’s extraordinarily high mechanical and thermal load carrying capacity, through which productivity of machine tools can be significantly increased. The maintenance intervals of extruder gearboxes can be extended from five to ten years by using carbonitrided bearings made from Mancrodur.
Integrated in a linear actuator, Schaeffler’s planetary screw drives (PWG) make a convincing case with their power density, which the example of an electromechanical riveting press illustrates. Compared with pneumatic drive solutions, an increase of up to 100 percent in output and a much more flexible process control have been realized here.
Industry 4.0 – optimizing operation and maintenance
For the first time, Schaeffler will be presenting its TorqueTracking system, which is an Industry 4.0 solution package for industrial drives. With a combination of vibration analysis and torque measurement, the drive can be operated reliably and close to its maximum capacity while maintenance can be planned and carried out based on the load conditions. This generally means that intervals are extended and maintenance costs are thus reduced.
With the new ProLink condition monitoring system (CMS), Schaeffler will be presenting its new generation of a multi-channel system for the condition monitoring of complete production facilities using four to 16 channels, for example, in the paper and steel sectors or for machine tools. In addition, the ProLink CMS can be used as a universal gateway for connecting the sensor level with the control and management levels and even cloud applications.
Detailed press releases regarding the innovations that Schaeffler will be presenting at the Hannover Messe can be found in our press kit: www.schaeffler.com/press-kit/hannover-messe