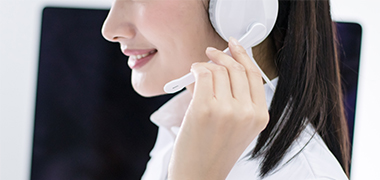
- Contact:Minister Xu
- Mobile:13841408476
- Tel:024-44837288
- Fax:024-44837004
- E-mail:xuming58@126.com
- Web:m.natashaterry.com
- Address:No.110 XiangHuai Road
Benxi Economic Development Zone
Liaoning Province
Automotive Adjustment
12 Jul,2019
The automotive industry is shifting for everyone, bearings manufacturers included. Here’s what you need to know to make sure you’re shifting with it.
The automotive industry has been prepping for a big shift for years now: the shift to electric transmissions. I doubt anyone’s a stranger to the discussion surrounding the direction the industry’s heading — after all, it’s had a perpetual place in the industry-wide discourse for years at this point. And during that time, the jump to electricbased transmissions has morphed from a conversation about “if” the industry would shift to a conversation about “when.”
But along with the increased certainty of that conversation, there’s one more important thing to talk about: how to shift with it. In Power Transmission Engineering, as well as our sister magazine, Gear Technology, we’ve already talked at length on numerous occasions about how this is going to affect gear manufacturing, most notably by drastically reducing the number of speeds, and therefore gears, needed per transmission. But the ever-mounting market pressure to switch to electrified powertrains is going to affect far more than just that.Gears may be ground zero for this particular shift in the industry landscape, but that doesn’t mean that other fields shouldn’t be paying attention, as well, and preparing to adjust accordingly.
“These changes will have an impact on the bearing industry as well,” Jitesh Modi, engineering director of transmission applications at Schaeffler, said. “The current 8/9/10 speed planetary automatic transmissions involve a large quantity of drawn and stamped bearing products like radial and thrust needle bearings. The drive units for electric vehicles mainly involve precision ground ball and roller bearings. The main performance requirements for these bearings are higher speeds, lower friction and NVH, improved power density and increased efficiency.”
So what are people working with bearings going to need to know to meet those shifting industry demands? Well, we sat down with Schaeffler to talk about what skills you might want to brush up on to make sure you’re ready to not just survive, but thrive in this changing market.
First, let’s talk about the shift itself. Ball and roller bearings are far from unknown in the automotive market. They’re currently seeing use primarily as main shaft and gear support bearings in more conventional transmissions, but according to Modi, they’re going to be rising to increased prominence and taking center stage along with electrified transmissions. And along with that comes a few extra design considerations bearing manufacturers will have to think around.
“Their application in electric vehicles, especially in electric motors,certainly requires design optimization and precision manufacturing to provide necessary running accuracy and desired performance at high speeds to an extent of 20,000 rpm and even above in the near future,” Modi said. “In addition, creep damage and electric current passage through bearings can pose additional challenges in electrified powertrains.”
As an example, Modi pointed to how the higher speeds in electric motors lead to an entire host of considerations that require manufacturers to focus on the bearing cage design. “The cage geometry, pocket clearance, cage guidance and its overall strength play an important role in bearing performance,”
Modi said. “For sealed bearings, the sealing design can influence bearing limiting speeds due to friction and heat generation. The seal wear can lead to grease leakage and subsequent bearing failures. The compatibility between sealing material and grease becomes a key consideration as well.”
While none of these factors are necessarily “new” considerations when designing a bearing, they’ll all require some reconsideration for electric transmission applications. Those higher speeds that electric motors run at will require sturdier, higher quality bearings alongside them. Much like it is for the gearing market, electrified transmissions will make increased quality demands of bearing manufacturers, and cage design is a primary method Modi pointed to meet those demands.
Bearing designers and manufacturers aren’t the only ones that are going to need to adjust to how the industry’s shifting. There will be a whole host of fresh demands placed on maintenance professionals and the aftermarket, as well, mostly in the form of new kinds of damage you might not be used to in bearings used in conventional transmissions.
On the maintenance side of the bearing market, however, Modi’s advice is pretty straightforward.
“Overall knowledge and understanding of typical bearing failures in electrified powertrains will be important for the maintenance professionals,” Modi said. “Familiarity with bearing diagnostic tools and techniques can be really helpful for efficient troubleshooting.”
The advice more or less amounts to “keep doing what you’re doing,” except in a slightly different field. But while the core competencies to get the job done might be the same, that doesn’t mean that maintenance professionals won’t have to learn something new. Much like with bearing design, the increased speeds and electrical currents running through these new powertrains can cause all manner of issues that you’ll need to brush up on. The electric current itself can induce craters or fluting damage in a bearing, and then, of course, there’s the already mentioned increased strain placed on the bearing cage due to the motor’s increased speed to worry about.
“The higher speeds of electric motors can lead to bearing cage failures if it is not designed suitably for the given speeds,” Modi said. “If electric motor bearings operate at high speeds with very low loads, bearing failures can result from skidding or slippage damage and also lead to NVH issues.”
Naturally, these are all issues a maintenance shop will be called on to handle. Some of these failure states aren’t usually present in conventional transmissions, but as electrified transmissions work towards becoming the norm, those unique problems will become more and more common thorns in the industry’s side — perhaps all the more so during the technology’s early years if manufacturers take a bit to get the cage design right.
Modi also pointed to a list of skills and knowledge sets that will be important for keeping competitive in the maintenance market in the future, citing “knowledge regarding bearing condition monitoring using vibration analysis, preload adjustment, seal wear and grease leakage, evaluation of mating parts and bearing damage analysis.”
For everyone involved, however, there are a few other non-bearing matters you might want to brush up on while you’re at it. Most obvious, make sure you understand how electric motors function, why they function the way they do, and their different industrial applications.
Sure, you might not make motors personally, but like with everything else in manufacturing, a bearing is only a single component of a much larger system, and how it fits into that larger system is important. Understanding the other components that bearing’s going to have to play with can go a long way towards helping design a quality part that will last for years — or, if the worst comes to happen and a part fails, understand what went wrong and why.
For other supplemental skills, Modi pointed to “assess ing the needs of condition monitoring, sensor technology, surface treatments and material technology advancements in the bearing industry.” While many of these skills might not be necessary to craft a quality bearing, Modi believes that they offer opportunities for valueadded integration into electrified powertrains. All those bells and whistles can be a genuine selling point if you can afford to include them, and having some of those extra credit competencies can open new avenues to finding your place in the market.
There is one last important thing to note: this article isn’t a blaring klaxon to get up and get moving. Judgment day is not dawning on the automotive market, and life will continue to go on. Electric transmissions are growing in importance, and will continue to do so, but we’re still years away from them becoming the primary force in the automotive market.
Even so, one can never get in on the ground floor too early when it comes to establishing oneself as a force in the industry, and major shifts like the push for electrification that create new opportunities to do just that don’t come every day. Competitiveness is a perpetually moving metric, and right now, that metric is moving in favor of electricpowered drivetrains. And while this isn’t a comprehensive checklist of what you’ll need to stay competitive in the years to come, it’ll hopefully at least do a little to get you thinking about how to move in lockstep with the times.