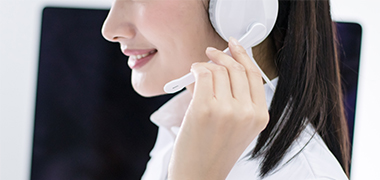
- Contact:Minister Xu
- Mobile:13841408476
- Tel:024-44837288
- Fax:024-44837004
- E-mail:xuming58@126.com
- Web:m.natashaterry.com
- Address:No.110 XiangHuai Road
Benxi Economic Development Zone
Liaoning Province
Machine Data Monitored Thanks to the New igus Communication Module
24 Jul,2019
With the isense name, igus offers a selection of products equipped with various types of sensors that detect the status of components such as cables or cable drag chains. Among other things, these sensors measure wear during operation and generate an alarm when it becomes necessary to schedule a repair or replacement. Interaction with the icom communication module allows data to be forwarded to an intelligent system. The module can be connected to all igus sensors .
It can, for example, collect data from sensors for measuring the friction or wear of the pin / hole connection of the cable chain, centralizing the data of the sensors that give indications on the traction / thrust forces and the data related to the monitoring of the cables. Once the sensor values are transmitted to the icom module, they must be "interpreted", ie included, in order to process and send appropriate instructions on how to intervene.
Until now, it was possible by connecting to the igus cloud. But due to the growing importance of IT security, more and more companies are choosing to build their own SCADA systems. For this reason, igus has perfected its "data concentrator" by developing the icom.plus version. With this evolved version, the customer can integrate the data of his plant in the way that best suits his needs.
The icom.plus system is programmed via igus online configuration systems based on initial algorithms related to the operating life. A big advantage is that, after the first online configuration, if the customer wishes, the module can work offline without the update function. In this "semi-offline" mode, for a short initial period, the device must be connected via IoT secure access to the igus server for an initial learning phase that will serve to adapt the calculation algorithms to the actual dynamic and environmental profile of the customer application.
In very restrictive areas, this phase can be managed completely "offline" through a storage medium. The user can decide how to use the form (and, therefore, his data) to benefit from the right balance between production optimization and IT security. The dynamic profile of the application, necessary for the calculation of the recommended maintenance, is obtained through the bus system of the machine directly from the control system.
Through the same route, information on the number of days up to the next recommended maintenance and signals related to any unusual changes in sensor data are transmitted to the SPS control system. The communication of information to the user takes place directly via the system monitor or through customer-specific SCADA systems.
With an online connection, the data relating to the duration of operation are continuously synchronized with the igus cloud: this allows you to optimize productivity, minimizing any risks of downtime. The data that is forwarded to the cloud is supported by billions of test cycles on energy chains and cables performed in the company laboratory. Thus, thanks to Machine Learning and KI, igus can provide precise information on the duration of the solutions used and inform the user in time if replacement is necessary.