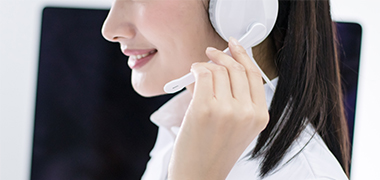
- Contact:Minister Xu
- Mobile:13841408476
- Tel:024-44837288
- Fax:024-44837004
- E-mail:xuming58@126.com
- Web:m.natashaterry.com
- Address:No.110 XiangHuai Road
Benxi Economic Development Zone
Liaoning Province
Igus Turns Bearings, Cables and Energy Chains into Smart Plastics
05 Aug,2019
Igus created the icom.plus module to connect the disparate data into one manageable system that tracks machine equipment. (Image source: igus)
Igus has created a system of data collection to monitor machine equipment with the goal of reducing downtime with a communication module connected to the company’s IT.
Manufacturers can significantly reduce machine maintenance needs while also reducing downtime costs by using smart machine components. Maintenance in the Industry 4.0 era has seen a paradigm shift. Plant personnel can continuously monitor a machine’s status so repair or replacement gets executed only when necessary, and the timing of maintenance tasks can be planned to avoid unexpected downtime.
Enter the Concept of Smart Plastics
Unplanned shutdowns and the cost of equipment failure can be greatly reduced by condition monitoring. Igus has developed a “smart plastics” predictive maintenance system that uses diverse sensors and monitoring modules for to track the condition of energy chains, plain bearings, linear bearings, and slewing ring bearings. The sensors in the system measure abrasion or wear of the pin/bore connections of energy chains. Sensors also detect breakages and the push/pull forces being applied. The system is networked with the igus communication module, icom.plus.
Igus uses the term smart plastics to describe the system of sensors that monitor the condition and performance of the equipment. “Smart plastics means companies have the capability to predict when maintenance will be required. Individual components such as energy chains and linear bearings can be monitored, so that preventive maintenance can be scheduled before the parts wear out completely,” Richard Habering, head of the Smart Plastics Business Unit at igus, told Design News. This reduces unplanned downtime, saving money for manufacturers.”
Flexible Data Integration Using icom.plus
Icom.plus is programmed with initial service-life algorithms based on igus configuration tools and, at the customer's request, can be operated offline without an update function after online installation. The user can therefore decide how the module is connected and how the data is managed, while establishing a balance between runtime maximization and IT security. If the user choses icom.plus, the service life information is continuously compared to use data in the igus cloud in order to enable maximum machine run times with a minimum risk of failure.
Igus created the module to connect the disparate data into one manageable system that tracks a range of equipment. “The igus communication module makes it possible to seamlessly integrate with a manufacturer’s IT infrastructure,” said Habering. “It allows for continuous monitoring and or automated triggering of in-house maintenance.”
Igus noted that the data in the cloud draws on the 10 billion annual test cycles of energy chains and cables performed in the company's 3,800 square meter test laboratory. The results of these tests are incorporated into igus’ service-life calculator so users can precisely predict how long an e-chain, for example, will work reliably in the respective machine tool application.
Isense Brings Together Diverse Sensors and Monitoring Modules
With the igus isense components, service-life is continually updated. Each update considers the current ambient conditions of the application. By incorporated machine learning and continuous improvement, the precise information on the durability of specific components in real applications can be obtained and reviewed against the manufacturer’s actual performance.
The isense system gathers data and integrates it into the user’s IT infrastructure. “An isense product includes diverse sensors and monitoring modules,” said Habering. “During ongoing operation, they detect the degree of wear or other degradations outside of normal operating standards and send an alarm as soon as repair or replacement is necessary. By networking with the icom.plus module, isense enables direct integration in the company-wide infrastructure.”
This data can be viewed on the screen of the machine control system. If an online connection is chosen, SMS or e-mail can provide critical details if unexpected operating states occur or maintenance is impending. Users are informed at an early stage if there is a need to procure replacement parts. A wide range of scenarios, such as automatic initiation of maintenance work or the ordering of replacement parts can be programed into the system.
How Do You Get the ROI?
Determining the return on investment (ROI) of predictive maintenance systems is as important as it is tricky. Yet it’s necessary in order to gain approval for the investment. “The ROI equation comes from calculating how much the company loses annually through unplanned downtime caused by the components in question,” said Habering. “By scheduling maintenance, customers can plan to maintain equipment during off or slow cycles. They would have to compare the annual cost of the smart plastics to the annual cost of unplanned downtime. In almost all cases, comparisons will prove that the limited additional costs of smart plastics will be far less than the costs for unplanned downtime.”