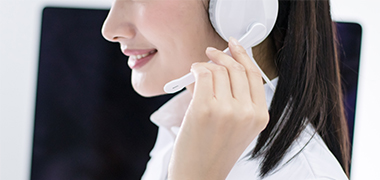
- Contact:Minister Xu
- Mobile:13841408476
- Tel:024-44837288
- Fax:024-44837004
- E-mail:xuming58@126.com
- Web:m.natashaterry.com
- Address:No.110 XiangHuai Road
Benxi Economic Development Zone
Liaoning Province
A coating for more reliable wind-turbine bearings
13 Aug,2019
It’s been said a wind turbine is only as good as its components, and a turbine’s bearings are extremely important ones. Although bearings are used many places throughout a nacelle, such as on generators and in the yaw and pitch system, those on main shafts and gearboxes are typically most problematic.
Timken ES302 is a thin-?lm, hard diamond-like carbon coating used to protect bearings. The ES302 coating uses a physical vapor-deposition technique that produces a vapor of material (which is then deposited on the object as a thin film) for an optimal level of friction reduction.
Not too long ago, wind operators and engineers began noticing a trend: roller bearings in turbine main shafts and gearboxes experienced premature damage, resulting in major rebuilds costing up to $300,000.
Bearings in turbines must withstand extreme environmental conditions, vibrations, and loads. What’s more is bearings are subject to combinations of dynamic loads that create high-contact stresses on rollers and raceways, which can lead to damage. These stresses are difficult to predict and challenge bearing manufacturers to develop new approaches to reducing premature wear.
“You never want the steel surfaces to touch in a bearing,” says Ryan Evans, director of research and development for bearings with The Timken Company. That seems like a tough demand because when you look at a roller bearing, you see rollers moving around in a tight space. But that’s the reason for lubrication — so there’s always a film between the roller and the inner raceway ring.”
Unfortunately, lubricant films are challenging to maintain consistently.
“So as engineers struggled to solve the steel-on-steel contact problems of a turbine’s bearings, a R&D team began developing a coating for roller bearings,” shared Evans.
Eventually, the team adopted a novel approach: making bearing rollers less “steel-like.” “We put a super-thin — fractions of a human hair thick — layer of a composite material on them,” says Evans. “It’s an engineered combination of ceramic and a polymer or, in other words, a plastic-like thin layer of material full of tiny ceramic particles.”
From this research, Timken’s ES302 coating was developed, which is a specially engineered nanostructure coating that aims to provide maximum durability where metal-on-metal contact occurs. To help wind-farm operators avoid unnecessary O&M costs, Timken can apply its ES302 coating to the rollers of main-shaft and gearbox bearings, resulting in a highly wear-resistant bearing that is ideal for low-speed, high-load applications.
Researchers first introduced ES302 in 2010 and conducted extensive analysis at the time that suggested an ES302-coated bearing (compared to an equivalent uncoated bearing) could experience up to six times greater life when operated in standard conditions, and up to three times greater life under debris-contaminated conditions in wind turbines.
Recently, these lab results were confirmed when an ES302-coated main-shaft spherical roller bearing was returned to the company (due to non-bearing-related issues) after seven years of service in a 1.5-MW wind turbine. Extensive laboratory analysis revealed the bearing would have continued to provide reliable, trouble-free operation into the 15 to 20-year time frame had it not been taken out of service.