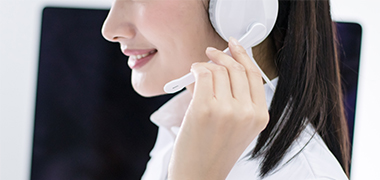
- Contact:Minister Xu
- Mobile:13841408476
- Tel:024-44837288
- Fax:024-44837004
- E-mail:xuming58@126.com
- Web:m.natashaterry.com
- Address:No.110 XiangHuai Road
Benxi Economic Development Zone
Liaoning Province
Linear Motion Q&A: Customized Machinery Built with Off-the-Shelf Components
20 Dec,2019
Machine builders strive to achieve the right balance of functionality, performance, price, durability, energy consumption and other attributes that will enable their products to excel against the competition. In the past, OEMs designed their machines around readily available standard components or had to add the cost and development time needed to obtain custom components designed especially for the application.
The growing breadth of standard offerings via the methodical evolution of electromechanical linear actuators, linear motion bearings, clutches and brakes, and linear slides now enable machine builders the benefit of a precisely matched “custom” solution while using cost-effective “standard” motion components.
Linear Slides and Stages James Marek, business unit manager What linear slides and stages are the most innovative in the marketplace? Why? Linear slides that meet the technical and commercial demands of customer needs are the most innovative in the marketplace. The demands that I constantly hear are enhancements to performance, the ability to perform in adverse environments and a quick “selection-to-delivery” cycle. Enhancements in performance include increased footprint-to-load capacity ratio and longer system lengths, along with improvement in positioning accuracies and repeatability. Linear slides are being deployed in adverse environments, and customers expect them to survive with little or no maintenance. Particularly challenging are environments where there are airborne contaminants that have a tendency to migrate into the linear guide system and ball screw. There are some novel sealing strategies that protect the internal components of the system. Engineering resources within organizations are leaner than ever. Web-based tools that allow them to do their job more efficiently are also in demand. There are tools that support not only the sizing of all components within the system but also output smart part numbers and CAD models.
How has linear slide and stage technology advanced in the past f ive years? There are a number of relatively new technologies that address the challenges associated with deploying a linear system in an application. These technologies address the mounting orientation, loading conditions, move profile and environmental conditions associated with customer applications. Extrusion technologies and post-processing of the extrusion have enabled systems of over 12 meters in length to be developed from a single piece of extrusion. In the case of a ball screw-driven system with long lengths, the system is often limited by the critical speed of the screw. A solution to this problem was to design screw supports that are dynamically transferred within the system at predefined locations. This has enabled 12 meter-long systems to rotate at input speeds of 3,000 rpm without hitting the critical speed of the screw. A number of unique sealing strategies have been developed to minimize particles and fluids from penetrating the interior components of a system. These seals allow linear systems to perform in paper and pulp, woodworking and painting applications.