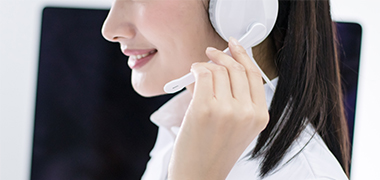
- Contact:Minister Xu
- Mobile:13841408476
- Tel:024-44837288
- Fax:024-44837004
- E-mail:xuming58@126.com
- Web:m.natashaterry.com
- Address:No.110 XiangHuai Road
Benxi Economic Development Zone
Liaoning Province
Schaeffler Goes Big in Bearing Applications
09 Mar,2020
One of the largest components manufactured by Schaeffler last year was a double-row tapered roller bearing featuring an outer diameter measuring 3.6 meters and a weight just over nine tons. This bearing is used to support the main shaft in an offshore wind turbine. Although this bearing is currently used in overseas markets, it is expected to be installed in North America-based applications later this decade.
Wind turbines equipped with bearings of this size certainly present some interesting challenges for application engineers and designers, according to Anant Bhat, business unit manager—railway and renewable energy, Schaeffler Group USA Inc.
“It is important to meet or even exceed several critical requirements such as contact pressure, rating life, safety factor as well as the actual reliability of the bearing and its components. This is where Schaeffler’s specially designed in-house calculation and simulation tools are invaluable: they assist our engineering and design team with the ability to provide comprehensive analysis support to help ensure optimum bearing design.”
Bhat said that Schaeffler’s production team can rely on several key manufacturing competencies including forging, soft machining, specially designed heat treatment, hard machining and final assembly for components like this. As a final manufacturing step, Schaeffler undertakes some of the industry’s most stringent quality inspections and measurements of the finished bearing that enable the company to ensure the highest quality and reliability for its customers throughout the world.
“In-house design validation and testing was performed on Schaeffler’s proprietary ASTRAIOS test stand, one of the largest, most modern and highest performing bearing test rigs in existence,” Bhat said. “ASTRAIOS simulates the real loads and moments that occur in a wind turbine, which enables Schaeffler to make a major contribution toward reducing development times for wind turbines. In doing so, ASTRAIOS facilitates a more reliable design process while also increasing the cost-effectiveness and safety of these massive powergenerating machines.” Along with projects in other industrial sectors, Schaeffler is currently working on additional bearings of similar size for main shaft applications in offshore wind turbines. In recent years, the company has gained a great deal of experience producing large components.
“In 2016, Schaeffler introduced the world’s first sealed ultralarge 241/1250 spherical roller bearing, which was specifically designed for the highest-capacity High Pressure Grinding Roll Crushers (HPGRs) used by the mining industry. The seal inside this massive roll support bearing is designed to prevent the crushing materials from contaminating its internal components,” Bhat said.
In 2019, Schaeffler produced the largest spherical plain bearing in the company’s history (to date). “Featuring an outside diameter of 1.9 meters, a bore diameter of 1.5 meters and a height of 60 centimeters, this special bearing weighs approximately 4.7 tons. It will be installed in a cutter suction dredger that is used in offshore oil & gas drilling applications,” Bhat added.
With each new bearing application, Schaeffler’s engineering and design team gains valuable experience and the tools necessary to provide reliable products for the areas like wind, mining and oil & gas no matter the size or scope.