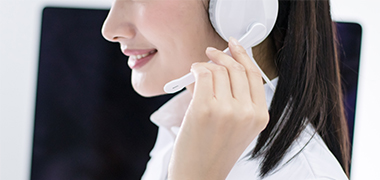
- Contact:Minister Xu
- Mobile:13841408476
- Tel:024-44837288
- Fax:024-44837004
- E-mail:xuming58@126.com
- Web:m.natashaterry.com
- Address:No.110 XiangHuai Road
Benxi Economic Development Zone
Liaoning Province
Schaeffler OPTIME makes condition monitoring affordable for all systems
23 Apr,2020
Comprehensive and automated condition monitoring is now becoming economical for maintenance engineers and plant operators: Schaeffler OPTIME offers an efficient and easy-to-use condition monitoring solution in the lower price segment, especially for indirectly process-critical aggregates of entire machine and plant fleets.
Schaeffler OPTIME: comprehensive and automated condition monitoring
Wireless IoT solution, expandable at any time
Several hundred units can be easily integrated in one day
Up to 50 percent lower costs compared to manual offline measurement
For cost reasons, only process-critical machines are usually permanently monitored in the production environment. In the process and automation industry, it is not uncommon for up to 95 percent of the units to be monitored either not at all or only based on routes using manual measurements. Comprehensive and automated condition monitoring is now becoming economical for maintenance engineers and plant operators: Schaeffler OPTIME offers an efficient and easy-to-use condition monitoring solution in the lower price segment, especially for indirectly process-critical aggregates of entire machine and plant fleets.
Automated data analysis with Schaeffler know-how
OPTIME is an easily expandable system and basically consists of wireless, battery-operated vibration sensors, a gateway and an app for visualizing the analysis results. The data captured by the sensors are analyzed using specially developed algorithms. The algorithms are based on Schaeffler's knowledge, the physical models that have been developed over decades and the condition monitoring experience from the rolling bearing service. With a lead time of several weeks, OPTIME recognizes damage to the respective components of, for example, electric motors, fans and pumps, as well as unbalance, incorrect alignment and stops. The app visualizes trends, the severity of incidents using traffic light colors, alarms and other information. The units can be grouped as required and their status can be displayed in different views for the user groups. Specific recommendations for action make it easy for in-house maintenance personnel or service companies to plan maintenance measures, personnel deployment and spare parts procurement in good time and cost-effectively.
Simple and quick commissioning
Maintenance engineers do not need any condition monitoring knowledge for installation and commissioning. Several hundred measuring points can be set up within a day. The vibration sensors are screwed or glued to the units and activated via near-field communication (NFC) via the app. All sensors connect independently with each other and with the gateway to form an independent mesh network, which is currently one of the most reliable and energy-saving IoT networks in the industry. In the mesh network, the sensors transmit raw vibration and temperature data as well as KPIs of the aggregates to the Schaeffler IoT hub via the gateway. This is where the data analysis takes place and the results are sent to the app for output on a wide variety of end devices by maintenance and plant operators. Alternatively, the results for integration into the customer's IT environment can be made available via a REST API interface.
Up to 50 percent cost savings
Compared to monthly offline measurements with handheld devices, OPTIME can achieve cost savings of around 50 percent. At the same time, compared to most wireless online CMS, the system offers higher quality monitoring with complex, algorithm-based analysis. If OPTIME is also used to monitor the large number of units for which condition monitoring has so far not been economical, a comprehensive view of the machine status is achieved for the first time, which includes all subsystems and also auxiliary units. Unscheduled downtimes of machines and systems can only be reliably avoided if the status of all assets is recorded and tracked automatically.