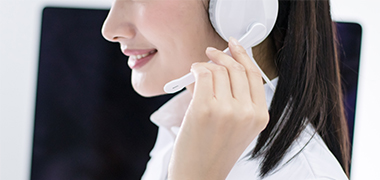
- Contact:Minister Xu
- Mobile:13841408476
- Tel:024-44837288
- Fax:024-44837004
- E-mail:xuming58@126.com
- Web:m.natashaterry.com
- Address:No.110 XiangHuai Road
Benxi Economic Development Zone
Liaoning Province
NSK Develops New Machine Tool Spindle Bearing Technology
28 Jan,2021
New roller-guided cage improves spindle productivity and reliability.
NSK Ltd. has developed a new machine tool bearing technology that makes spindle assembly easier, reduces run-in time, and also improves reliability. Easier assembly and higher reliability achieves lower maintenance burden and higher productivity. NSK will be exhibiting the technology at “NSK VIRTUAL EXPO - Machine Tool Online Exhibition” from January 25 - February 26. Moving forward we will be discussing the technology and related products with our partners and customers to gage demand and other needs, and will work toward starting wide-scale production in fiscal 2021.
Development Background
When assembling a spindle, grease lubrication of single-row cylindrical roller bearings requires a time-consuming run-in process to optimize internal grease amount and position. This is a productivity bottleneck calling for a new solution. On the other hand, when using oil-air lubrication*1, the temperature of single-row cylindrical roller bearings can rise abnormally during low-speed rotation, which is another area that needs improvement.
Ideally, these problems would be addressed by using bearings with roller-guided cages to stabilize the cage position during operation, but conventionally this method resulted in the cage bearing excessive force and becoming damaged more easily. As a result, until now, spindle bearings have typically used outer ring riding cages.
*1 Oil-air lubrication: A lubrication method in which compressed air mixed with a small amount of lubricant is blown into the bearing at high speed.
Features of New Technology
1. Significant reduction of grease run-in time.
NSK has developed a roller-guided cage with equivalent durability to conventional outer-ring-guided cages. The new roller-guided cage design expels excess lubricant more effectively and shortens run-in time. Grease run-in time is up to 70% shorter than conventional outer-ring-guided cages.
2. Lower temperature rise under oil-air lubrication
Roller-guided cage bearings face the issue of abnormal temperature rise caused by excessive retention of lubricating oil inside the bearing during low speed operation. However, the new cage design solves this issue and reduces excessive oil retention and temperature rise during low speed operation. This contributes to enhancing the stability and reliability of spindles operating with oil-air lubrication.
3. High reliability roller-guided cage
Cage design and material have been optimized to prevent failure/breakage. As a result, the durability (reliability) of the new roller-guided cage is significantly increased compared to conventional roller-guided cages.
Benefits
This technology contributes to improved productivity at machine tool makers by reducing the assembly/run-in time of grease-lubricated spindles. The technology also improves cage strength and reduces temperature rise under oil-air lubrication thereby contributing tog high reliability operation.
Applications
In built-in motor spindles used in machining centers for automotive parts and general machine parts, cylindrical roller bearings are used on the rear side of the spindle because the heat generated by the spindle itself causes axial expansion. NSK’s new technology is ideal for bearing on the rear side of the spindle.