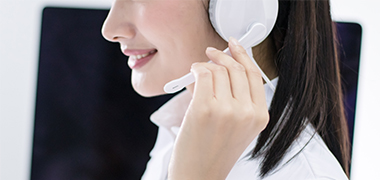
- 聯(lián)系人:許部長
- 聯(lián)系電話:13841408476
- 固定電話:024-44837288
- 公司傳真:024-44837004
- E-mail:xuming58@126.com
- 公司網址:m.natashaterry.com
- 地 址:遼寧省本溪經濟開發(fā)區(qū)香槐路110號
大型軋機軸承座的鑄造工藝改進
2024-01-29摘 要:針對軸承座鑄件冒口間的縮松缺陷, 采用集中補縮的工藝措施將分散小冒口改為單獨大冒口, 并利用MAGMA軟件進行凝固模擬分析,生產了優(yōu)質的軸承座鑄件。經生產驗證,改進后的冒口工藝不僅消除了鑄件的縮松缺 陷,而且鑄件質量穩(wěn)定。
支撐輥軸承座是軋機的關鍵零件之一,服役條件惡劣,長期處在高溫、高強度沖擊力的環(huán)境下工作,要求鑄件具備良好的綜合力學性能[1]。軸承座在鑄造過程中容易出現縮孔、疏松、裂紋、氣孔等缺陷,從而影響鑄件的使用性能。同時,由于受設備能力、工藝裝備、作業(yè)環(huán)境等諸多因素的影響,厚大鑄件在制造過程中經常因為夾雜物、縮松、晶粒粗大等缺陷導致探傷不合格[2]。因此,通過鑄造工藝的改進減少厚大鑄件的鑄造缺陷,減少鑄件的返修,提高鑄件的質量具有十分重要的意義。
1、軸承座的技術要求
軋機支撐輥軸承座鑄件,其輪廓尺寸為1850mm×1708mm×854mm,壁厚為136mm,壁厚為617mm,鑄件重15500kg。鑄件質量的要求主要包括化學成分、力學性能、無損檢驗等。鑄件材料執(zhí)行德國標準DIN17182中GS-20Mn5+N,其化學成分和力學性能如表1、表2。鑄件要求整體進行超聲波探傷和磁粉探傷,其超聲波探傷按照標準EN12680-level2執(zhí)行,磁粉探傷按照標準EN1369-LM2/AM2/SM2執(zhí)行。
2、鑄造工藝設計及改進
2.1分型面
根據軸承座的結構特點,采用上、中、下三箱造型。下箱采用實樣造型,中箱采用抽芯實樣和組芯的復合造型,上箱采用蓋箱造型。下箱與中箱采用定位銷的方法,中箱與上箱采用定位線的方法合箱,保證型腔的尺寸精度。
2.2造型材料
鑄鋼件的澆注溫度高,而且軸承座的壁厚為617mm,壁厚為136mm,所以采用耐火度較高的鉻鐵礦砂作為面砂,防止鑄件在凝固過程中發(fā)生粘砂缺陷。在鑄型表面涂刷3~5遍醇基鋯英粉涂料,每次刷完后用砂紙打磨光滑再涂刷下一遍,保證涂料的厚度到達約2mm。選擇鉻鐵礦砂和鋯英粉涂料的使用,不但有效地減少鑄件表面粘砂,而且鑄件的表面質量顯著提高。
2.3澆注系統(tǒng)
鋼液的澆注溫度高、流動性差、易氧化,因此要求快速、平穩(wěn)充型。鑄造工藝設計中選取澆注系統(tǒng)為開放式澆注系統(tǒng),使用鋼液上升速度計算法計算該鑄件澆注系統(tǒng)各單元的尺寸,其中鋼包孔、直澆道、橫澆道、內澆道的截面積比例A水口∶A直∶A橫∶A內=1.0∶2.25∶2.5∶3.0。采用底注式+切線式的澆注方式,底注式可以使內澆道從鑄件底面引入,保證鋼液在型腔內平穩(wěn)上升;同時切線式內澆道使鋼液在型腔內旋轉,有利于浮砂、氣體、夾雜物等進入冒口,減少鑄件缺陷的產生。整個澆注系統(tǒng)均采用高鋁耐火磚管連接,采用底注包澆注,澆注溫度控制在1550~1560℃。
2.4冒口設計
2.4.1原冒口工藝
由于軸承座屬于厚大鑄件,在4個角的位置都存在分散的熱節(jié),在鑄件凝固過程中容易出現縮孔、縮松缺陷。在鑄造工藝設計時依據模數法、熱節(jié)圓法設計冒口大小,在熱節(jié)處分別設置明冒口,在兩個大熱節(jié)處設置一個的腰圓式冒口,冒口尺寸大小Y750mm×950mm、澆高1000mm;在兩個小熱節(jié)處分別設置圓形冒口,冒口直徑大小準700mm、澆高1000mm。原冒口工藝方案見圖1。
分散冒口的工藝方案首批生產 4 件軸承座,超 聲波探傷合格率低,其中 3 件軸承座在兩個冒口之 間發(fā)現缺陷,距離分型面100~150 mm范圍內。經分析缺陷為縮松, 生產時采用焊接的方式進行修 復,但是縮松缺陷的焊接難度大,大大增加了生產成本,同時也面臨著鑄件報廢的風險。
2.4.2冒口工藝的改進
為了消除冒口間的縮松缺陷,提高鑄件的探傷合格率,減少鑄件的焊補返修,改進了軸承座的冒口工藝方案。在軸承座的內孔上方設置一個單獨的圓形冒口,冒口尺寸準1100mm、澆高900mm,并將內孔局部鑄實作為補貼。采用集中補縮代替分散補縮的工藝思路改進了冒口工藝方案,即為1個大冒口取代3個小冒口,同時改進前和改進后的冒口重相當不會造成成本增加,改進后的冒口工藝方案見圖2。
2.5凝固模擬
凝固模擬可以預測鑄件的縮孔、縮松的位置,有利于鑄造工藝驗證和優(yōu)化,對降低生產成本和提高鑄件質量方面起著很大的作?。針對軸?座改進前和改進后的冒口工藝方案,利用MAGMA凝固模擬軟件分別進行模擬分析,其模擬結果見圖3、圖4。通過模擬結果的對比分析:改進冒口的方案更有利于冒口的集中補縮,冒口中的鋼液更能長時間地保持在高溫狀態(tài),使冒口與鑄件之間形成了明顯的溫度梯度,實現鑄件的順序凝固,提高了冒口的補縮效果。
2.6改進效果
采用改進冒口的工藝共生產了4批24件軸承座,鑄件在砂型內保溫結束后打箱清砂,熱處理消除鑄造應力后切割?口,冒口根部組織致密。軸承座粗加工后進行超聲波探傷檢驗,鑄件內部組織致密均沒有發(fā)現縮孔、縮松缺陷,而且鑄件質量穩(wěn)定。
3、結論
針對批量生產的軸承座,通過對鑄造工藝的研究,并運用 MAGMA 模擬軟件對軸承座進行凝固過程模擬,采用大冒口集中補縮代替小冒口分散補縮的工藝優(yōu)化,使冒口與鑄件形成了明顯的溫度梯度, 實現鑄件的順序凝固。經生產驗證,改進冒口的工藝方案消除了鑄件的縮孔、縮松缺陷,提高了鑄件的質 量, 為今后生產類似鑄件的鑄造工藝方案具有一定的指導意義。
來源:鑄造技術
(版權歸原作者或機構所有)