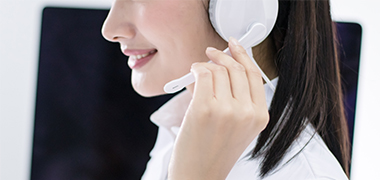
- 聯(lián)系人:許部長
- 聯(lián)系電話:13841408476
- 固定電話:024-44837288
- 公司傳真:024-44837004
- E-mail:xuming58@126.com
- 公司網(wǎng)址:m.natashaterry.com
- 地 址:遼寧省本溪經(jīng)濟開發(fā)區(qū)香槐路110號
冷連軋工作輥表面剝落原因分析
2024-07-26廖耀俊,趙賢平
冷軋軋輥是冷連軋機組重要大型零部件,其制造工藝相對復(fù)雜且工作環(huán)境惡劣,承受摩擦、熱應(yīng)力、沖擊等應(yīng)力作用,在使用過程中可能會產(chǎn)生斷裂、剝落、磨損等,進而失效,增加耗材成本并影響生產(chǎn),造成經(jīng)濟損失。某公司不銹鋼生產(chǎn)線在正常軋制生產(chǎn)過程中冷連軋工作輥突然表面剝落,造成故障停機,嚴(yán)重影響了正常生產(chǎn)。本文以該冷連軋工作輥剝落樣品為分析對象,通過宏觀斷口、光譜成分測定、硬度、金相組織、掃描電鏡等理化檢測手段,結(jié)合日常使用狀況,分析探討軋輥表面剝落原因。
1、理化檢驗結(jié)果
剝落塊斷口觀察
對軋輥剝落塊進行宏觀形貌分析(見圖1)。剝落塊上存在典型的疲勞斷口特征,中心圓圈區(qū)域能觀察到明顯的貝紋線,是疲勞擴展區(qū)的重要特征;貝紋線圓心處為疲勞源,是疲勞裂紋的萌生區(qū),可以看出疲勞源位于軋輥內(nèi)部而非表面;外圈區(qū)域所占面積最大,宏觀形貌呈放射線狀,是瞬時斷裂區(qū)。結(jié)構(gòu)材料與機械零件失效案例中,疲勞破壞有別于靜載破壞,大多是在無預(yù)警且不可預(yù)期的情況下發(fā)生,失效前外觀沒有明顯的征兆,損傷嚴(yán)重。
使用掃描電鏡觀察疲勞源區(qū)域發(fā)現(xiàn),存在直徑約50μm顆粒狀夾雜物,EDS結(jié)果顯示其含有Ca、K、O、Mg、Al、Si等元素(見圖2),為大顆粒氧化物混合型夾雜物。
化學(xué)成分在剝落塊上切取試樣進行光譜成分分析,該軋輥材質(zhì)為8Cr3NiMoV。檢測結(jié)果見表1,除Cr元素略低于下限,其它成分均在標(biāo)準(zhǔn)GB/T1299-2014范圍內(nèi)。使用洛氏硬度計測試剝落塊硬度,硬度(HRC)值達(dá)到64.5,且試樣上各位置較均勻,符合標(biāo)準(zhǔn)要求。
金相觀察
使用線切割機在疲勞源處截取金相試樣,經(jīng)測量,疲勞源距軋輥表面約8mm;制樣拋光后,利用ZEISSImager.A1m金相顯微鏡、ZEISSEVO18掃描電子顯微鏡等儀器進行觀察分析。發(fā)現(xiàn)剝落塊中存在多條呈根須狀裂紋(見圖3),裂紋起源于內(nèi)部疲勞源位置,向軋輥表面擴展。
全面觀察試樣發(fā)現(xiàn),剝落塊中存在較多的塊狀夾雜物(見圖4a),尺寸達(dá)90μm,夾雜物嚴(yán)重超標(biāo)。使用掃描電子顯微鏡能譜分析(見圖4b),塊狀大顆粒夾雜物主要為O、Al,少量Mg、S、Ca、Mn、Fe,可以推斷是以Al2O3為主要成分的混合型夾雜物??赡苁巧a(chǎn)軋輥時熔煉工藝控制不嚴(yán)所致。
2、分析與討論
裂紋產(chǎn)生過程
從宏觀形貌分析可以推斷,軋輥剝落失效起源于內(nèi)部疲勞源,隨后在工作中不斷承受循環(huán)的應(yīng)力作用下,裂紋逐漸擴展形成貝紋線;疲勞裂紋擴展到一定程度造成強度不足,無法承受軋制過程中的外力作用,最終形成終斷區(qū),軋輥表面剝落。軋輥在工作過程中,由于軋機的負(fù)荷以及軋輥在接觸點上的局部擠壓,造成的最大組合剪切應(yīng)力位于軋輥表面之下的某個較小區(qū)域中。軋輥在制造和使用前的準(zhǔn)備工序會產(chǎn)生殘余應(yīng)力,同時雖然冷軋加工溫度低,但是軋輥和帶鋼在摩擦力作用下溫度也會升高產(chǎn)生熱應(yīng)力。若軋制過程中發(fā)生斷帶、甩尾、 重疊、打滑等,將使軋輥表面受到局部過載熱及沖擊應(yīng)力。由于非金屬夾雜物以機械混合物的形式存在于鋼中,而其性能又與鋼有很大差異,破壞了鋼基體的均勻性、連續(xù)性,并在該處造成應(yīng)力集中,而成為疲勞源。另外,在升溫過程中,非金屬夾雜物和基體的線膨脹系數(shù)不同,在夾雜物附近的基體中產(chǎn)生一個附加的應(yīng)力場。在這種復(fù)雜的應(yīng)力條件下,如果表面層存在非金屬夾雜物,特別是脆性夾雜物,則在球形夾雜物最大應(yīng)力的兩個極端處首先與基體剝離,形成初生的顯微裂紋;裂紋在迅速擴展之前,鋼基體與夾雜物的交界處逐漸與基體分離,連成裂紋通道。隨著應(yīng)力循環(huán)次數(shù)的增加,顯微裂紋沿著球的外殼撕裂基體逐漸向外擴展,當(dāng)裂紋整體尺寸超過軋輥能承受的臨界尺寸時,疲勞裂紋進入失穩(wěn)擴展階段,軋輥表面最終因發(fā)生瞬時斷裂而剝落。軋輥表面剝落經(jīng)歷了由夾雜物導(dǎo)致的裂紋萌生→裂紋擴展→ 剝落幾個過程。
夾雜物對疲勞性能的影響
夾雜物對工件疲勞壽命的影響與夾雜物的性質(zhì)、大小、數(shù)量、分布有關(guān)。一般來說,硬而脆與基體聯(lián)結(jié)性較差且不變形的塊狀或球狀夾雜物,如TiN、Al2O3等比具有延展性、細(xì)長類夾雜物危害更大。當(dāng)夾雜物數(shù)量較多、聚集分布時或處于零件表層、高應(yīng)力區(qū)時,對疲勞壽命影響最嚴(yán)重。同時夾雜物對疲勞性能的影響另外也取決于基體的組織和性質(zhì),實驗指出,軟鋼的疲勞強度和夾雜物的關(guān)系較小,隨著鋼的強度提高,夾雜物的有害影響就越來越嚴(yán)重。在具有高硬度和高強度的金屬材料中,夾雜物對疲勞強度的影響成為比較突出的問題。
根據(jù)相關(guān)研究資料表明,疲勞壽命對夾雜物的尺寸非常敏感,減少夾雜物的尺寸,可以顯著地提高疲勞壽命。對于高硬度、高強度工件,表面夾雜物的臨界尺寸為8~10μm,并且隨著硬度的增加而減小、隨著所處深度增加而增加。夾雜物小于臨界尺寸,可避免夾雜物引起的疲勞斷裂,疲勞性能會更好;當(dāng)夾雜物大于臨界尺寸時,隨著夾雜物尺寸的增加,鋼的疲勞強度與疲勞壽命急劇降低。據(jù)文獻指出,對于高強度鋼,如果夾雜物尺寸減小1/3,疲勞壽命將延長10倍,如果夾雜物尺寸減少大約一半,疲勞壽命將延長100倍。同時,如果夾雜物尺寸減少一半,疲勞強度可提高1.12~1.15倍。
綜上所述,該軋輥是在使用過程中復(fù)雜應(yīng)力作用下,在大尺寸夾雜物處產(chǎn)生疲勞裂紋源,隨著交變應(yīng)力的不斷變化,疲勞裂紋擴展并產(chǎn)生次生裂紋,在斷口表面形成疲勞條帶和放射狀條帶。當(dāng)裂紋整體尺寸超過臨界尺寸時,疲勞裂紋進入失穩(wěn)擴展階段,軋輥最終因發(fā)生瞬時斷裂而剝落失效。
3、結(jié)論
(1)該冷連軋工作輥表面剝落是由近表面大尺寸Al2O3類脆硬夾雜物引起的疲勞斷裂。
(2)加強對軋輥的檢測,超聲波檢測可探測內(nèi)部的缺陷,磁粉和渦流可檢驗表面缺陷;根據(jù)情況采用不同方法或相結(jié)合,確保軋輥質(zhì)量。
(3)制定科學(xué)合理的軋輥使用與維保制度,確保使用過程中的冷卻與潤滑,防止過熱。
來源:《柳鋼科技》
(版權(quán)歸原作者或機構(gòu)所有)