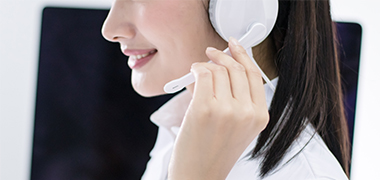
- 聯(lián)系人:許部長
- 聯(lián)系電話:13841408476
- 固定電話:024-44837288
- 公司傳真:024-44837004
- E-mail:xuming58@126.com
- 公司網(wǎng)址:m.natashaterry.com
- 地 址:遼寧省本溪經(jīng)濟開發(fā)區(qū)香槐路110號
軸承套圈的常見缺陷及預防措施
2022-12-12作者:郭浩 來源:軸承雜志社
軸承套圈每個生產(chǎn)工序均會對其質(zhì)量產(chǎn)生影響。軸承失效分析中,套圈的材料孔洞缺陷、鍛造缺陷、熱處理質(zhì)量、磨削燒傷、環(huán)境腐蝕是導致軸承失效的主要原因,因此必須重視套圈的生產(chǎn)質(zhì)量,減少軸承因套圈質(zhì)量問題而導致的早期失效,Z終實現(xiàn)提高軸承壽命的目的。
對廢品分析軸承套圈產(chǎn)生缺陷的原因進行統(tǒng)計發(fā)現(xiàn):材料因素是影響套圈質(zhì)量的主要因素,包括材料內(nèi)部冶金缺陷,如夾雜物、夾渣、顯微孔隙,套圈因材料外部缺陷未完全清除的殘留,如脫碳、微裂紋、表面缺陷等;其次為熱處理工藝,包括熱處理質(zhì)量不合格(組織粗大,屈氏體不符合標準要求,粗大網(wǎng)狀碳化物)和淬火應力裂紋;另外,磨削質(zhì)量也是影響套圈質(zhì)量的主要因素之一,主要為磨削燒傷引起表層組織改變,嚴重時產(chǎn)生磨削裂紋;管理因素(人為原因)主要是指套圈生產(chǎn)過程中操作不當引起的機械傷(劃傷、墊傷)以及環(huán)境腐蝕(酸腐蝕和氧化腐蝕),提高操作人員的責任意識及業(yè)務水平可以預防此類缺陷的產(chǎn)生。
1、套圈常見質(zhì)量問題及特征
1.1 材料質(zhì)量缺陷
材料質(zhì)量缺陷是決定軸承套圈質(zhì)量的重要因素。套圈的材料主要有棒材和鋼管。按照缺陷產(chǎn)生的部位,將材料質(zhì)量缺陷分為內(nèi)部缺陷和外部缺陷。
1.1.1 內(nèi)部缺陷
內(nèi)部缺陷主要有非金屬夾雜物、夾渣、顯微孔隙、發(fā)紋等。
非金屬夾雜物是軸承鋼冶煉過程產(chǎn)生的,無法避免,因此GB/T 18254—2016對軸承鋼非金屬夾雜物有特殊規(guī)定。非金屬夾雜物存在于套圈基體內(nèi),成為裂紋源造成套圈早期剝落;加工過程中偶爾會裸露套圈表面,造成套圈報廢。磨削滾道面的非金屬夾雜物裸露形貌如圖1所示。
圖1 外圈溝道面非金屬夾雜物殘留電鏡形貌
套圈存在肉眼可見的夾雜物即夾渣(主要成分為爐渣或耐火材料)時,易成為裂紋源,使套圈過早損壞甚至報廢。外圈外徑面的夾渣缺陷如圖2所示。
圖2 外圈外徑面夾渣缺陷
顯微孔隙又稱顯微裂紋,金相觀察其沿晶界分布并沿軋制方向伸展。產(chǎn)生原因主要有材料中心疏松或加熱溫度過高,鋼坯心部的低熔點合金相熔融。若套圈中存在顯微孔隙,會極大降低晶粒間的結(jié)合力,影響套圈的力學性能;嚴重的顯微孔隙淬火時容易產(chǎn)生裂紋,若暴露至軸承零件表面則易產(chǎn)生黑點,降低防銹性能甚至導致軸承產(chǎn)生疲勞剝落。外圈顯微孔隙金相圖如圖3所示。
圖3 外圈顯微孔隙金相形貌
發(fā)紋是一種存在于鋼材表皮下層的細小裂紋缺陷。產(chǎn)生原因為鋼錠中的皮下氣泡或非金屬夾雜物經(jīng)軋制變形后,存在于材料表層且沿軋制方向斷續(xù)分布,數(shù)量不等。若套圈存在發(fā)紋缺陷,易產(chǎn)生剝落掉塊。
1.1.2 外部缺陷
外部缺陷主要有材料裂紋、脫碳、凹坑等。
材料裂紋存在于棒材表層一定深度下,折疊裂紋的特征是與表面呈一定角度,裂紋中一般有氧化皮存在,裂紋兩側(cè)有脫碳現(xiàn)象。若材料裂紋在套圈中殘留必定引起質(zhì)量問題。在套圈車削成形過程中,若材料裂紋缺陷沒有完全車除,便會在套圈上殘留,Z終造成后續(xù)加工或裝配或使用過程中開裂。內(nèi)圈外徑面鋼管裂紋殘留如圖4所示。
圖4 車削成形后內(nèi)圈外徑面鋼管裂紋殘留
材料表面脫碳,若是鋼管,主要產(chǎn)生在外圈外徑面及滾道面擋邊處和內(nèi)圈內(nèi)、外徑面,分別對應鋼管的外徑面和內(nèi)徑面;若是棒材,材料表面脫碳指鋼材外表面。脫碳對套圈質(zhì)量的影響與裂紋相似,一方面套圈淬火時易產(chǎn)生淬火應力裂紋;另一方面,脫碳區(qū)拉應力較大,受外力作用易開裂,因此,GB/T 1255—2014對軸承套圈表面脫碳層深度進行了嚴格的控制。外圈外徑面殘留鋼管原始脫碳層如圖5所示。
圖5 外圈外徑面殘留鋼管原始脫碳層
材料表面缺陷,如較深的銹蝕坑、壓痕等,若車削成形時不能完全去除,亦會在套圈表面殘留,影響其加工質(zhì)量。
1.2 加工成形缺陷
套圈制造方式不同,其成形工藝不同。僅對工作中遇到的套圈成形缺陷問題進行分析。
1.2.1 鍛造工藝
鍛造是軸承套圈常見的加工工藝。鍛造可以細化晶粒,改善網(wǎng)狀碳化物,從而提高套圈性能。然而,若鍛造工藝不當會產(chǎn)生鍛造缺陷,影響套圈質(zhì)量。如G95Cr18不銹軸承鋼,鍛造溫度過高易產(chǎn)生孿晶組織,這是標準JB/T 1460—2011嚴格控制的。常見的鍛造缺陷主要有鍛造組織過熱、過燒和鍛造折疊裂紋。
鍛造過熱組織會沿晶界析出粗大而封閉的網(wǎng)狀碳化物,嚴重的網(wǎng)狀碳化物會破壞材料的連續(xù)性,使鋼的力學性能降低,特別是沖擊韌性,而且其在退火中保持不變,只能通過正火才能消除。
過燒組織晶粒粗大,晶界局部氧化或熔融,主要原因是加熱溫度過高或保溫時間過長等。GCr15軸承鋼鍛造過?產(chǎn)生的熔融孔洞形貌如圖6所示。
圖6 鍛造過燒熔融孔洞形貌(×200)
鍛造折疊裂紋是由于切料不齊、毛刺或操作不當?shù)仍谔兹Ρ砻嫘纬?,其特征是裂紋一般與表面呈一定角度,裂紋兩側(cè)有嚴重的脫碳層。粗磨外圈折疊裂紋形貌如圖7所示。
圖7 外圈鍛造折疊裂紋形貌
1.2.2 車削工藝
車削是軸承套圈成形的主要缺陷:一方面是不能完全清除材料表面缺陷,使套圈表面殘留,進而影響套圈質(zhì)量;另一方面是較深切尖銳的車刀紋極易產(chǎn)生應力集中甚至燒傷,在淬火時產(chǎn)生淬火應力開裂,裝配時產(chǎn)生斷裂。其主要產(chǎn)生于套圈油溝及滾道面擋邊處。外圈滾道擋邊的裂紋缺陷如圖8所示,原因是擋邊存在車削燒傷。
圖8 外圈滾道面擋邊車削缺陷(×500)
1.2.3 冷輾及串光工藝
冷輾成形也是軸承套圈常見的成形方式,冷輾工藝不當造成的套圈質(zhì)量缺陷主要為冷輾裂紋。冷輾屬于冷加工,材料延展性有限,若輾擴較大,易產(chǎn)生冷輾裂紋,另外,GCr15軸承鋼由于存在碳化物帶(碳化物偏析聚集),此處組織硬且脆,在變形過程中易拉裂。沿碳化物帶分布的冷輾裂紋缺陷形貌如圖9所示。
圖9 沿碳化物帶分布的冷輾裂紋形貌
串光是改變套圈表面粗糙度的一種方法,其工藝不當易造成薄壁套圈產(chǎn)生磕碰傷甚至掉塊,如圖10所示。
圖10 串光工藝不當所致的擋邊掉塊
1.3 熱處理缺陷
熱處理(主要指淬、回火工藝)是實現(xiàn)軸承套圈高強韌性的重要工藝,對套圈質(zhì)量的影響較大。統(tǒng)計數(shù)據(jù)表明,熱處理質(zhì)量缺陷約占套圈廢品的22.55%。常見的熱處理質(zhì)量缺陷主要有脫碳、淬火應力裂紋、組織過熱及屈氏體不合格。
熱處理脫碳是指套圈淬回火過程中表層碳含量低于正常含量,可分為完全脫碳和脫貧碳。完全脫碳時套圈表層為鐵素體組織,金相下呈白色;脫貧碳時該區(qū)域馬氏體針相對基體較粗大,但均為馬氏體組織。隨著熱處理設備的改進,套圈淬回火時主要產(chǎn)生脫貧碳現(xiàn)象,會極大降低套圈表層的耐磨性和耐疲勞性能,局部產(chǎn)生拉應力,是微裂紋源區(qū)。
嚴重的熱處理脫碳會產(chǎn)生淬火應力裂紋,其特征是形狀不規(guī)則,深淺不一,裂紋開口處多存在油污,金相觀察裂紋兩側(cè)無脫碳現(xiàn)象。
套圈組織過熱主要因加熱溫度過高或保溫時間過長而產(chǎn)生粗大的馬氏體針。
屈氏體不符合標準要求主要是指加熱不足引起塊狀屈氏體或冷卻不良形成針狀屈氏體,宏觀表現(xiàn)為局部軟點即硬度不合格。外圈表面嚴重熱處理脫碳組織形貌如圖11所示,其在裝配時開裂。
圖11 外圈熱處理脫碳組織形貌
1.4 磨削缺陷
磨削是軸承加工過程的關鍵工序,是實現(xiàn)套圈精度尺寸要求的重要加工工藝。根據(jù)統(tǒng)計結(jié)果,磨削質(zhì)量缺陷主要指磨削燒傷、磨削裂紋及其他磨?缺陷。磨削燒傷指表層組織燒傷(高溫回火),降低表面耐磨性;磨削裂紋導致套圈開裂,整批報廢,經(jīng)濟和時間損失巨大。
軸承套圈磨削燒傷常見于滾道面、內(nèi)外徑面以及端面,其特征是內(nèi)外徑面及滾道面呈振紋狀或斑塊狀,端面燒傷多呈斑塊狀。磨削燒傷冷酸洗后呈灰黑色,金相觀察組織呈暗黑色。磨削燒傷冷酸洗組織形貌如圖12所示。
圖12 套圈磨削燒傷冷酸洗組織形貌
磨削裂紋多為龜裂狀,深度較淺,金相觀察裂紋兩側(cè)無脫碳現(xiàn)象。磨削裂紋常伴有嚴重的磨削燒傷,但磨削燒傷不一定產(chǎn)生磨削裂紋。套圈磨削過程中,其表層應力狀態(tài)較復雜,磨削裂紋的產(chǎn)生是綜合應力的結(jié)果,因此分析其產(chǎn)生原因時需綜合考慮,尤其是磨削前各工序的加工質(zhì)量,如車削質(zhì)量、熱處理變形等。外圈內(nèi)徑面熱酸洗磨削裂紋形貌如圖13所示。
圖13 外圈內(nèi)徑面熱酸洗磨削裂紋形貌
1.5 裝配質(zhì)量缺陷
裝配質(zhì)量缺陷包括人為因素導致的磕碰傷或擠壓傷,裝配工藝不當導致套圈局部受力較大,產(chǎn)生變形甚至斷裂,套圈保管或操作不規(guī)范會引起腐蝕及異物污染等。除裝配工藝不當外,裝配質(zhì)量缺陷多為人為因素,而這是可以避免的。裝配過程中外圈局部掉塊如圖14所示。
圖14 裝配過程中外圈局部掉塊形貌
1.6 管理因素
管理因素主要指套圈各加工工序過程中由于人為因素引起的套圈機械傷(擠壓傷、磕碰傷、劃傷)以及腐蝕現(xiàn)象(酸蝕和銹蝕),其中以套圈腐蝕Z為常見,占套圈廢品比例約為10%。腐蝕現(xiàn)象在套圈滾道面Z為常見,其特征呈單一或者簇狀點狀缺陷(偶爾呈線狀),嚴重時呈凹坑狀;另外,軸承各個加工工序過程均有可能產(chǎn)生腐蝕現(xiàn)象。腐蝕現(xiàn)象雖受環(huán)境影響較大,但若操作規(guī)范完全可以避免。外圈滾道面點狀腐蝕缺陷形貌如圖15所示。
圖15 外圈溝道面點狀腐蝕缺陷形貌
2、預防措施
1)加強材料質(zhì)量檢驗。根據(jù)統(tǒng)計分析,目前國內(nèi)軸承鋼質(zhì)量主要存在的問題為表面缺陷,其次為非金屬夾雜物。尤其注意與設計及車加工結(jié)合,車除多余的材料缺陷;同時,控制夾雜物尺寸,少數(shù)尺寸較大的夾雜物是應力集中點,易產(chǎn)生微裂紋,若分布在表面則造成套圈廢品或早期損壞;Z后,碳化物不均勻性會影響套圈的熱處理質(zhì)量,造成力學性能不均,也會影響后續(xù)磨削加工(如熱處理變形磨削時易產(chǎn)生磨削燒傷)。?過加強材料檢驗,從源頭減少軸承套圈產(chǎn)生質(zhì)量問題的概率。
2)優(yōu)化軸承套圈加工成形工藝。優(yōu)化熱處理工藝,減少套圈產(chǎn)生組織過熱或欠熱以及脫碳現(xiàn)象,盡量避免淬火應力裂紋產(chǎn)生。優(yōu)化車削工藝,避免產(chǎn)生尖銳的車刀紋以及尖角毛刺等。同時,根據(jù)套圈尺寸要求,盡可能多地車除材料原始缺陷。優(yōu)化磨削工藝,避免產(chǎn)生磨削燒傷和磨削裂紋。
3)提高操作人員的責任意識和操作能力,以避免套圈產(chǎn)生機械傷及腐蝕現(xiàn)象,同時減少軸承安裝不當(局部偏載、未對準等)的裝配問題。
作者:郭浩,雷建中,王玉良,扈林莊
來源:《軸承》(節(jié)選)
本文引用格式:
郭浩,雷建中,王玉良,等.軸承套圈的常見缺陷及預防措施[J].軸承,2019(1):66-71.